Common ERP Implementation Mistakes and How to Avoid Them
Enterprise Resource Planning (ERP) systems are designed to streamline and automate business processes across an organization. ERP software helps organizations to manage their operations, financials, and supply chain more effectively, leading to improved efficiency and cost savings. However, implementing an ERP system can be a complex and challenging process, and there are several common ERP implementation mistakes and how to avoid them.
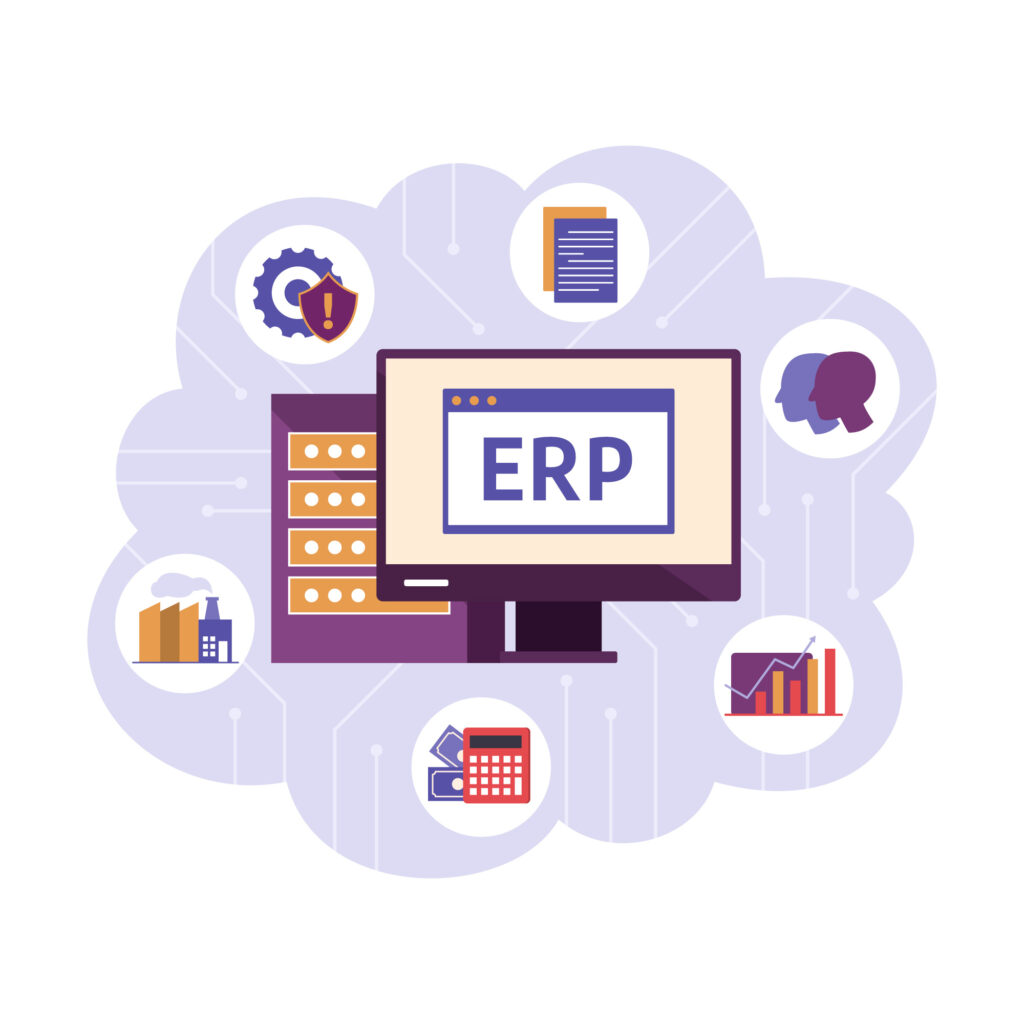
1. Lack of Planning
One of the most common mistakes that organizations make when implementing an ERP system is the lack of planning. Implementing an ERP system is a complex project that requires careful planning, coordination, and communication across multiple teams and departments. Organizations need to have a clear understanding of their requirements, goals, and expectations before they start the implementation process. This includes developing a project plan, setting timelines, and identifying key stakeholders and resources.
To avoid this mistake, organizations should create a detailed project plan that outlines the objectives, milestones, and timelines for the implementation. They should also identify the key stakeholders and resources needed for the project and allocate them accordingly. It is also important to communicate the project plan and progress regularly with stakeholders to keep them informed and engaged.
2. Inadequate Testing
Another common mistake that organizations make is inadequate testing of the ERP system before going live. Testing is a crucial part of the implementation process, and it ensures that the system is functioning as expected and meets the organization’s requirements. Inadequate testing can lead to costly errors and downtime, which can negatively impact the organization’s operations and reputation.
To avoid this mistake, organizations should conduct comprehensive testing of the ERP system before going live. This includes functional testing, performance testing, and user acceptance testing. They should also involve end-users in the testing process to ensure that the system is easy to use and meets their needs. It is also important to address any issues or bugs that are identified during testing promptly.
3. Insufficient Training
Another common mistake is insufficient training for end-users. ERP systems are complex and require specialized knowledge and skills to use effectively. End-users need to be trained on how to use the system to perform their daily tasks, access information, and generate reports. Insufficient training can lead to user frustration, errors, and reduced productivity.
To avoid this mistake, organizations should invest in comprehensive training programs for end-users. This includes training on the system’s functionality, data entry, reporting, and troubleshooting. It is also important to provide ongoing support and resources to users after the system goes live to ensure that they are comfortable using the system and can perform their tasks effectively.
4. Resistance to Change
ERP implementation often involves changes in business processes, organizational structure, and culture. Resistance to change is a common mistake that can impede the implementation process and reduce the benefits of the system. Resistance to change can come from employees who are comfortable with existing processes, fear of job loss, or lack of understanding of the benefits of the system.
To avoid this mistake, organizations should communicate the benefits of the ERP system to employees and involve them in the implementation process. Employees should be provided with training and support to adapt to the new system and its processes. It is also important to address any concerns or questions that employees may have about the implementation process.
5. Poor Data Quality
ERP systems rely on accurate and up-to-date data to function effectively. Poor data quality is a common mistake that can negatively impact the system’s performance and accuracy. Poor data quality can come from inadequate data entry procedures, duplicate data, or inconsistent data formats.
To avoid this mistake, organizations should establish data entry procedures that ensure the accuracy and completeness of data. They should also invest in data cleansing and data management tools to identify and eliminate duplicate data and inconsistencies. It is also important to establish data governance policies and procedures to ensure ongoing data quality and maintenance.
6. Over-customization
ERP systems are designed to meet the needs of a wide range of organizations and industries. However, some organizations may try to customize the system to meet their specific needs. Over-customization is a common mistake that can lead to increased implementation time, complexity, and cost. Over-customization can also make it difficult to upgrade the system or apply patches and fixes.
To avoid this mistake, organizations should carefully evaluate their requirements and identify areas where customization is necessary. They should also consider the long-term implications of customization, such as maintenance and upgrades. It is important to balance customization with the system’s out-of-the-box functionality and best practices to ensure that the system remains stable, scalable, and supportable.
7. Inadequate Vendor Support
ERP systems are typically supported by the software vendor or a third-party service provider. Inadequate vendor support is a common mistake that can lead to system downtime, slow response times, and increased costs. Inadequate vendor support can come from poor communication, lack of expertise, or insufficient resources.
To avoid this mistake, organizations should carefully evaluate the vendor’s support services and ensure that they meet their requirements. This includes evaluating the vendor’s expertise, response times, and escalation procedures. It is also important to establish clear communication channels and expectations with the vendor to ensure that issues are addressed promptly and effectively.
Conclusion
ERP implementation is a complex process that requires careful planning, coordination, and communication. Common mistakes, such as lack of planning, inadequate testing, insufficient training, resistance to change, poor data quality, over-customization, and inadequate vendor support, can negatively impact the implementation process and reduce the benefits of the system. By avoiding these mistakes and following best practices, organizations can successfully implement an ERP system that improves efficiency, reduces costs, and supports growth and innovation.
Related Articles: